Stirling engine with rhombic drive 75 ccm
Stirling engine with rhombic drive 75 ccm
Hi all,
after reading a lot in this beautiful Stirling forum I want to show you my own work on the topic.
Its a 75 ccm Rhombic Stirling with finned heat exchangers and regenerator, completely dry-running.
Still unpressurized because a lot things have to be improved before.
The main challenge at this stage seems to be the balance between friction and compession, a lot of sets of piston rings and rod seals have been made without really satisfying results.
Andy Ross stated that the piston has to hold most of the pressure for 5 seconds in tests. Can you confirm this ? I am far away from 5 seconds with acceptable friction.
If someone has ideas on this special topic I would be very interested.
At the moment I prefer 6 rings for the working piston and 4 rings for the displacer piston all streched by a regular spring (1 spring for 2 rings).
For the rod seal I use at the moment 6 plain bushes with a small distance as a labyrinth type.
With this configuration I measured 12 Watts with a simple prony brake, max free speed is 1600 1/min.
I know this is very low for an engine of this size but a lot of things have to be improved and will hopefully raise performance.
Here are two links to Youtube videos of the engine:
http://youtu.be/BdJAMC8nfZI
http://youtu.be/jUyZeJFdO64
I am always happy for comments and suggestions and will report more if you are interrested.
Greetings
Ralf
after reading a lot in this beautiful Stirling forum I want to show you my own work on the topic.
Its a 75 ccm Rhombic Stirling with finned heat exchangers and regenerator, completely dry-running.
Still unpressurized because a lot things have to be improved before.
The main challenge at this stage seems to be the balance between friction and compession, a lot of sets of piston rings and rod seals have been made without really satisfying results.
Andy Ross stated that the piston has to hold most of the pressure for 5 seconds in tests. Can you confirm this ? I am far away from 5 seconds with acceptable friction.
If someone has ideas on this special topic I would be very interested.
At the moment I prefer 6 rings for the working piston and 4 rings for the displacer piston all streched by a regular spring (1 spring for 2 rings).
For the rod seal I use at the moment 6 plain bushes with a small distance as a labyrinth type.
With this configuration I measured 12 Watts with a simple prony brake, max free speed is 1600 1/min.
I know this is very low for an engine of this size but a lot of things have to be improved and will hopefully raise performance.
Here are two links to Youtube videos of the engine:
http://youtu.be/BdJAMC8nfZI
http://youtu.be/jUyZeJFdO64
I am always happy for comments and suggestions and will report more if you are interrested.
Greetings
Ralf
Re: Stirling engine with rhombic drive 75 ccm
Ralf, why use piston rings, these rely on pressure against the cylinder wall fur their seal, you might be better with no rings, a close fit, and labyrinth sealing ie., a number of groves in the piston skirt.
If this is a BETA type, what are the rings on the displacer for? Are they there to divert the air through a coaxial regenerator, if so, I'd say no rings, design the displacer with a taper, smaller at the hot end (1 mm to 1.5 mm gap in cylinder), larger at the cold end, sliding fit.
One type of ring that works quite well is made of Teflon. A strip of Teflon sheet about 1 mm thick, cut to say 6 mm wide, wrap it round the piston in the groove, the end should be either cut at 45*, or like a step, only 1 ring needed.
What is the piston and cylinder made of?
Ian S C
If this is a BETA type, what are the rings on the displacer for? Are they there to divert the air through a coaxial regenerator, if so, I'd say no rings, design the displacer with a taper, smaller at the hot end (1 mm to 1.5 mm gap in cylinder), larger at the cold end, sliding fit.
One type of ring that works quite well is made of Teflon. A strip of Teflon sheet about 1 mm thick, cut to say 6 mm wide, wrap it round the piston in the groove, the end should be either cut at 45*, or like a step, only 1 ring needed.
What is the piston and cylinder made of?
Ian S C
Re: Stirling engine with rhombic drive 75 ccm
Hi Ian,
I use piston rings because the engine is completely dry-running and for a long-lasting performance this seems for me to be the only way.
I tried a solid graphit piston which sealed beautifully perfect but friction was to high and without doubt it wouldnt´t stand longer then 100 hours.
Pressure of the rings against the cylinder walls is obtained by the springs and works not so bad, the main problem is the displacerpiston connecting rod sealing.
I experimented with different teflon qualities virginal, some filled with glass, some with carbon and others but it was not satisfying.
Now I use a plastic bearing compound specially for dry running against stainless steel Igus Iglidur W300.
So material of the cylinder liner is of stainless and the piston is of alu (hence it has no contact).
The rings on the displacer are to ensure that all swept air travels through the exchangers and regenerator.
Maybe I don´t understand you properly, I would be very happy if you can show me an alternative or other tips.
Thanks for your kind respose and hope th read more ..
Greetings
Ralf
I use piston rings because the engine is completely dry-running and for a long-lasting performance this seems for me to be the only way.
I tried a solid graphit piston which sealed beautifully perfect but friction was to high and without doubt it wouldnt´t stand longer then 100 hours.
Pressure of the rings against the cylinder walls is obtained by the springs and works not so bad, the main problem is the displacerpiston connecting rod sealing.
I experimented with different teflon qualities virginal, some filled with glass, some with carbon and others but it was not satisfying.
Now I use a plastic bearing compound specially for dry running against stainless steel Igus Iglidur W300.
So material of the cylinder liner is of stainless and the piston is of alu (hence it has no contact).
The rings on the displacer are to ensure that all swept air travels through the exchangers and regenerator.
Maybe I don´t understand you properly, I would be very happy if you can show me an alternative or other tips.
Thanks for your kind respose and hope th read more ..
Greetings
Ralf
Re: Stirling engine with rhombic drive 75 ccm
Nicely done tom-rock,
My hat off to you
It will be interesting to see what happens when you get around to pressurising your engine (keep us posted). This should reduce effect of relative ring friction when compared to the potential increased power gains.
Just out of interest, have you considered Rulon for your rings?
You may have seen these, but here are some deconstruction/cut-away pictures of 2 commercial free piston Beta configurations that reveals their sealing approach...
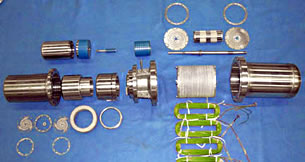

Thanks for sharing your hard work!
vamoose
My hat off to you

It will be interesting to see what happens when you get around to pressurising your engine (keep us posted). This should reduce effect of relative ring friction when compared to the potential increased power gains.
Just out of interest, have you considered Rulon for your rings?
You may have seen these, but here are some deconstruction/cut-away pictures of 2 commercial free piston Beta configurations that reveals their sealing approach...
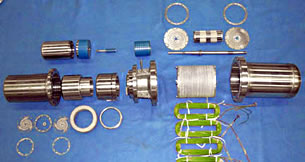

Thanks for sharing your hard work!
vamoose
Re: Stirling engine with rhombic drive 75 ccm
One could try self lubricating carbon graphite rings with a chrome plated cylinder. Several companies sell these.
Some of the very long lasting Free Piston Stirling Engines use gas bearings. These are essentially very small notches that allow for a very small layer of air to pass on either side of the piston. However, this is extremely hard to machine. Sun Power uses these, and they have a tested lifespan over 10 years and a predicted lifespan around 40 years.
If you're feeling adventurous, you could try to obtain the ANL near frictionless, super-hard carbon coating. It has 40 times less friction than teflon, and its wear rate is so low that its lifespan will be over 10 years with continuous use. Stirling Motors was trying to use this stuff. Stuff is apparently great for bearings too.
http://www.transportation.anl.gov/features/1998_rd.html
http://www.azom.com/news.aspx?newsid=4186
http://www.transportation.anl.gov/mater ... tings.html
Some of the very long lasting Free Piston Stirling Engines use gas bearings. These are essentially very small notches that allow for a very small layer of air to pass on either side of the piston. However, this is extremely hard to machine. Sun Power uses these, and they have a tested lifespan over 10 years and a predicted lifespan around 40 years.
If you're feeling adventurous, you could try to obtain the ANL near frictionless, super-hard carbon coating. It has 40 times less friction than teflon, and its wear rate is so low that its lifespan will be over 10 years with continuous use. Stirling Motors was trying to use this stuff. Stuff is apparently great for bearings too.
http://www.transportation.anl.gov/features/1998_rd.html
http://www.azom.com/news.aspx?newsid=4186
http://www.transportation.anl.gov/mater ... tings.html
Re: Stirling engine with rhombic drive 75 ccm
Stainless steel is ok for the cylinder, but aluminium is a no no, a light weight/hollow cast iron piston that will just slide through the cylinder under it's own weight is about the cheapest way. With a graphite piston the cylinder must be honed to a high polish, and if you get it right the piston will last for years. I would go for the cast iron, have another look in my album, you will find a piston there, it is 30 mm diameter, the skirt is 1 mm thick, and the crown is 3 mm thick, this is the piston from the stove top fan. The cylinder is made from the tube from the inside of a car shock absorber (good things for getting materials from when you learn how to open them), this is round, parallel, and polished ready to use.
The ideal cylinder for a graphite piston is made of glass, see reference to Airpot, these cylinders are for door closers, and (from what I understand) if you live in USA you can obtain one as a free sample, complete with fitted piston. Ian S C
The ideal cylinder for a graphite piston is made of glass, see reference to Airpot, these cylinders are for door closers, and (from what I understand) if you live in USA you can obtain one as a free sample, complete with fitted piston. Ian S C
Re: Stirling engine with rhombic drive 75 ccm
Hi all,
many thanks for your kind comments, there are a lot of interesting ideas and suggestions.
I will try pressurising the engine as soon as I improved the other obviously weak points friction, compression and regenerator.
The engine is prepared for pressurization up to ten bar, just the seals are not inserted and the cranshaft seal is not ready designed I only built in a cartridge which can be filled later.
I just think step by step and now I can better see what is an improvement and what not when the power is low and the engine is less complicated.
Or do you think the behaviour of the engine is so different when pressurized that I better pressurize it now and optimize then?
I will also check the heat exchangers with FastTrack gas path design from the new book of Allan J Organ which seems to be a much better way to optimize them as the second order method I used so far.
I just need some time to read and understand it properly to use it right. At the moment it is more fun to work practically on the engine then reading and studying theoretics.
Rulon is also teflon-based and the new sealing material I use now seems to be much better then any teflon compounds.
Free piston engines are really a neat and elegant way of design, but have many other challenges to handle them.
But maybe one of the next engines will be a free piston engine, its a really nice thing.
I experimented with graphite, it really seals beautifully and friction was good but it is so fragile and always it looses dust which is everywhere so I cant believe it can be suitable for a long lasting engine of reasonable power.
Gas bearings as I understand are really high tech and to complicated to manufacture so they are no option for me , correct me if I am wrong.
The ANL near frictionless, super-hard carbon coating sounds really nice but is also very high tech and I didn´t found any prizes or offers and I think they won´t deal with my pistons which I send from germany to them for a prize acceptable for me ( e. g. 100 $ or something like this per part, and I would need many of them for serious optimization ...).
The aluminium of the pistons of course never touches the cylinders. All guidance is made by the split rings which are tensed by the springs. I thought this is very often made this way, or am I wrong ?, do you think I should use additional elements to guide the piston in the cylinder ? (which will cause additional friction which as I learned is the most important thing to avoid)
Shock absorber components and other pre-manufactured parts mostly don´t suit and I don´t want to design all around them, when ever possible I make the parts by myself from bar stock the effort is second-rate.
Same with Airpot or other glass elements, they are fragile and have very different coefficents of thermal expansion so it is difficult to attach them to the other components.
All bigger engines with reasonable power output I studied had piston rings.
Do you really think a close-fitting piston without rings can obtain a high power, long lasting Stirling engine ?
I thought the problems of wear, different coefficents of thermal expansion and imperfect alignment of the drive mechanism (which causes execessive friction when you rely on close fitting pistons) and the absence of pre-loaded tension won´t give you any room.
Sorry, a lot of text and I hope you understand what I want to say, my english is not the best. So please ask if you don´´t understand anything it might be explained wrong.
I am really open to any suggestions I just mentioned my point of view and hopefully you continue interest.
Many greetings
Ralf
many thanks for your kind comments, there are a lot of interesting ideas and suggestions.
I will try pressurising the engine as soon as I improved the other obviously weak points friction, compression and regenerator.
The engine is prepared for pressurization up to ten bar, just the seals are not inserted and the cranshaft seal is not ready designed I only built in a cartridge which can be filled later.
I just think step by step and now I can better see what is an improvement and what not when the power is low and the engine is less complicated.
Or do you think the behaviour of the engine is so different when pressurized that I better pressurize it now and optimize then?
I will also check the heat exchangers with FastTrack gas path design from the new book of Allan J Organ which seems to be a much better way to optimize them as the second order method I used so far.
I just need some time to read and understand it properly to use it right. At the moment it is more fun to work practically on the engine then reading and studying theoretics.
Rulon is also teflon-based and the new sealing material I use now seems to be much better then any teflon compounds.
Free piston engines are really a neat and elegant way of design, but have many other challenges to handle them.
But maybe one of the next engines will be a free piston engine, its a really nice thing.
I experimented with graphite, it really seals beautifully and friction was good but it is so fragile and always it looses dust which is everywhere so I cant believe it can be suitable for a long lasting engine of reasonable power.
Gas bearings as I understand are really high tech and to complicated to manufacture so they are no option for me , correct me if I am wrong.
The ANL near frictionless, super-hard carbon coating sounds really nice but is also very high tech and I didn´t found any prizes or offers and I think they won´t deal with my pistons which I send from germany to them for a prize acceptable for me ( e. g. 100 $ or something like this per part, and I would need many of them for serious optimization ...).
The aluminium of the pistons of course never touches the cylinders. All guidance is made by the split rings which are tensed by the springs. I thought this is very often made this way, or am I wrong ?, do you think I should use additional elements to guide the piston in the cylinder ? (which will cause additional friction which as I learned is the most important thing to avoid)
Shock absorber components and other pre-manufactured parts mostly don´t suit and I don´t want to design all around them, when ever possible I make the parts by myself from bar stock the effort is second-rate.
Same with Airpot or other glass elements, they are fragile and have very different coefficents of thermal expansion so it is difficult to attach them to the other components.
All bigger engines with reasonable power output I studied had piston rings.
Do you really think a close-fitting piston without rings can obtain a high power, long lasting Stirling engine ?
I thought the problems of wear, different coefficents of thermal expansion and imperfect alignment of the drive mechanism (which causes execessive friction when you rely on close fitting pistons) and the absence of pre-loaded tension won´t give you any room.
Sorry, a lot of text and I hope you understand what I want to say, my english is not the best. So please ask if you don´´t understand anything it might be explained wrong.
I am really open to any suggestions I just mentioned my point of view and hopefully you continue interest.
Many greetings
Ralf
Re: Stirling engine with rhombic drive 75 ccm
Hi,
power is much increased and an Arduino is added to measure engine data.
I added a new video with many updates at this link:
https://youtu.be/k3XNxzmMoWI
Ralf
power is much increased and an Arduino is added to measure engine data.
I added a new video with many updates at this link:
https://youtu.be/k3XNxzmMoWI
Ralf
-
- Posts: 308
- Joined: Tue Feb 08, 2011 2:29 pm
- Location: Brokeville, NY. USA
Re: Stirling engine with rhombic drive 75 ccm
Ralf,
Are the Tc and Te related to gas temperatures? If those are the temperature differences of the working fluid, you should see much higher power output.
Are the Tc and Te related to gas temperatures? If those are the temperature differences of the working fluid, you should see much higher power output.
Re: Stirling engine with rhombic drive 75 ccm
Hi Aviator,
on which calculations is your statement based?
When I use the basic Beale equation just to estimate the power output of a carefully designed engine :
P = Bn*Pm*f*V0
where
Bn = Beale number = 0,15 for a professional designed Stirling (average of commercial engines) , a high Temperature difference is contained
Pm = mean gas pressure = 200000 Pa = 2 bar (as I wrote the heat exchangers are not able to deliver enough heat for more than 2 bar pressure, which will be the next big improvement the 5 bar in the video is just for demonstration)
f = frequency = 33,33 1/s = 2000 1/ min
V0 = swept volume of working (compression) Piston = 7,2 * 10power-5 cubicmeter (D = 5,6 cm)
Then I get P = 72 Watt, so my 50 Watt don´t look so bad (remember: compared with a professional engine) I think.
Greetings Ralf
on which calculations is your statement based?
When I use the basic Beale equation just to estimate the power output of a carefully designed engine :
P = Bn*Pm*f*V0
where
Bn = Beale number = 0,15 for a professional designed Stirling (average of commercial engines) , a high Temperature difference is contained
Pm = mean gas pressure = 200000 Pa = 2 bar (as I wrote the heat exchangers are not able to deliver enough heat for more than 2 bar pressure, which will be the next big improvement the 5 bar in the video is just for demonstration)
f = frequency = 33,33 1/s = 2000 1/ min
V0 = swept volume of working (compression) Piston = 7,2 * 10power-5 cubicmeter (D = 5,6 cm)
Then I get P = 72 Watt, so my 50 Watt don´t look so bad (remember: compared with a professional engine) I think.
Greetings Ralf
-
- Posts: 308
- Joined: Tue Feb 08, 2011 2:29 pm
- Location: Brokeville, NY. USA
Re: Stirling engine with rhombic drive 75 ccm
I have a big problem with the Beale number. Have you ever wonder how those stirling "pioneers" came up with the number? Answer. With stirling engines they designed and built, and those designs are supposedly optimum(or no one else will ever come up with a better design). I have spend a good part of the past 12 months looking for the stirling engine or engines that they used to for the Beale calculation. Guest what, I found none. Maybe I have not looked careful enough. I do want to see one of their designs used for the Beale number calculation.
BTW. Andy Ross' this stirling engine is 100cc (a bit larger than yours), running at a bit more than 1 bar, and produces 230w. The Beale number must went through the roof.
https://www.youtube.com/watch?v=BlI3_QoU3Rs
The problem Ralf is that when I asked around. No one can tell what exactly the hot and cold temperatures are. All they can tell is heater and cooler temperatures. Guest what, those are not the hot and cold temperatures of the working fluid.
BTW. Andy Ross' this stirling engine is 100cc (a bit larger than yours), running at a bit more than 1 bar, and produces 230w. The Beale number must went through the roof.
https://www.youtube.com/watch?v=BlI3_QoU3Rs
The problem Ralf is that when I asked around. No one can tell what exactly the hot and cold temperatures are. All they can tell is heater and cooler temperatures. Guest what, those are not the hot and cold temperatures of the working fluid.
Re: Stirling engine with rhombic drive 75 ccm
Hi Aviator,
the engine of Andy Ross you mentioned delivers 230 W with 2,7 bar pressure, which ends up in a Beale number of normal range.
Comprehensive explanation of the Beale number you will find in older literature e.g. I have the book of Colin West "Principles and Applications of Stirling Engines" [1986] which has several tables of engines and their Beale numbers with real power and the derived of the Beale equotation.The Engines are all of the "benchmark" Engines as GPU3,V160 the Philipps engines and also the engines of A. Ross you mentioned and many more.
And the power prediction of the Beale number fits very good to the real, measured power.
It is very basic but neverthless a good guideline.
Ralf
the engine of Andy Ross you mentioned delivers 230 W with 2,7 bar pressure, which ends up in a Beale number of normal range.
Comprehensive explanation of the Beale number you will find in older literature e.g. I have the book of Colin West "Principles and Applications of Stirling Engines" [1986] which has several tables of engines and their Beale numbers with real power and the derived of the Beale equotation.The Engines are all of the "benchmark" Engines as GPU3,V160 the Philipps engines and also the engines of A. Ross you mentioned and many more.
And the power prediction of the Beale number fits very good to the real, measured power.
It is very basic but neverthless a good guideline.
Ralf
-
- Posts: 308
- Joined: Tue Feb 08, 2011 2:29 pm
- Location: Brokeville, NY. USA
Re: Stirling engine with rhombic drive 75 ccm
On the video he said 230w @ 25psi.
Oh yeah. The GPU3 and the V160, they have to be designed right because they are commercially built. All the Beale number tells you is if build a stirling engine the same way as those, you can estimate the power output with a simple formula.
Oh yeah. The GPU3 and the V160, they have to be designed right because they are commercially built. All the Beale number tells you is if build a stirling engine the same way as those, you can estimate the power output with a simple formula.
Re: Stirling engine with rhombic drive 75 ccm
Hi,
in his book A. Ross writes on several places 230 W at 2,7 bar for this engine and also in third party literature I found this value.
And you are right with the Beale number, thats why they are called the benchmark engines.
But when I look at the effort they made in research and development in these days I think it would be very hard to develop a better engine in the future for any company even with the aid of computers they didn´t had.
The performance or efficiency of these engines weren´t the problem, just the cost was.
Ralf
in his book A. Ross writes on several places 230 W at 2,7 bar for this engine and also in third party literature I found this value.
And you are right with the Beale number, thats why they are called the benchmark engines.
But when I look at the effort they made in research and development in these days I think it would be very hard to develop a better engine in the future for any company even with the aid of computers they didn´t had.
The performance or efficiency of these engines weren´t the problem, just the cost was.
Ralf
Re: Stirling engine with rhombic drive 75 ccm
Hi guys. I think you saw this already, but to clarify for other readers because this could be important: 2.7 atmospheres is indeed 25 psi, as the first atmosphere is neutral and isn't normally counted in psi.
Bumpkin
Bumpkin