large lamina flow build
Re: large lamina flow build
Please visit the following link -
http://heetgasmodelbouw.ridders.nu/Webp ... ameset.htm
http://heetgasmodelbouw.ridders.nu/Webp ... ameset.htm
Re: large lamina flow build
Thanks! As far as regenerator goes, I am using ss wool in the heat tube. I have the tube filled 2/3 full. I have not tried it without it yet.Tom Booth wrote:Wow! congratulations on getting it running!Out of curiosity, are you using any kind of regenerator ?
Last edited by derwood on Wed Feb 27, 2013 6:08 pm, edited 1 time in total.
Re: large lamina flow build
Thanks for the input Ian.IanSC wrote:derwood, had a look at your vidio, I wounder if a better weight distribution on your flywheels might help for a starter. It could be done by drilling a hole near the end of each arm, and put a bolt in, and add extra weight, this would be the equivalent of having a rim on the wheels, its out there where the weight is required. The bearings, have you removed the grease, and used light grade oil. I think you need to try a crank with adjustable throw, but you have to have some way of testing the power output, because as you reduce the stroke the speed should go up, but the torque may come down, you want the highest of both. Reduce the stroke by small amounts each time, you may find that the power output is fairly flat over quite a wide range. The vidio was quite good, but I could not get more than 4sec on my dialup, so I had to wait until I could get on Broadband. Ian S C
My flywheels are two strips of 1/4 in. x 1 in. steel welded at 90 degrees. I have several holes drilled out for different strokes and I have another with bolts welded on the ends. I add nuts to adjust weight. For bearings I am bushings machined from solid stock Polyethylene. It is self lubricating plastic comparable to teflon but it has a lower heat tolerance. Seems to work good. It seems that no matter what stroke I use, the performance and top speed is alway the same, just weaker. I even adjust the flywheel weight at each stroke. Start up time is about 5 min. As you can see in the video, It starts and takes off really good but it is like it runs into a brick wall. It refuses to accelerate. The torque seems to be quite high considering the low rpms. I have been getting conflicting results throughout my testing. Although I did switch to a new cylinder, which is a bit smaller. I tried to keep the conditions the same and make changes one at a time and test after each change. If the choke is an 1/8 in. smaller or bigger it won't run at all.
Re: large lamina flow build
derwood, it seems that these engines are sort of a constant speed thing (all different), and when they get going, it takes a lot to gert any thing different, at least you got it going. Ian S C
Re: large lamina flow build
Derwood
The Thermo Lag engine (Lamina flow, not that there is any laminar flow, it's all turbulet!) is not a constant speed engine. From the most recent tests on my engine (only 20cc) it will run from a few hundred rpm at about 40w input to 3150rpm when red hot, off load, as can be seen from the power curves, attached.
I am concerned, that because you are using sliding bearings rather than rolling element bearings, they are adding much more friction than you imagine. I'm seeing about 0.08w/cc so your engine at about 420cc will probably be producing, with it's limited heat exchanger, about 12 to 15w which will be absorbed easily by the sliding bearings. If I remove the piston and connecting rod from my engine and spin the crank by hand, it will run long enough for me to go into the house, put the kettle on, and return to the workshop to find it is still spinning.
I have no wish to hijack your thread but the following information may well be of value to you and others. The tests were to establish the effect of the 'Choke' on the engines performance and the results are quite enlightning. The best by far was the original cooler head with 80 x 1.2mm holes yet I was/am puzzled as to why the plain choke failed to improve the performance. Still thinking about the results!
Appologies for the quality of the graph, I had to photograph the computer screen as the forum won't accept a PDF file.
GeoffV
The Thermo Lag engine (Lamina flow, not that there is any laminar flow, it's all turbulet!) is not a constant speed engine. From the most recent tests on my engine (only 20cc) it will run from a few hundred rpm at about 40w input to 3150rpm when red hot, off load, as can be seen from the power curves, attached.
I am concerned, that because you are using sliding bearings rather than rolling element bearings, they are adding much more friction than you imagine. I'm seeing about 0.08w/cc so your engine at about 420cc will probably be producing, with it's limited heat exchanger, about 12 to 15w which will be absorbed easily by the sliding bearings. If I remove the piston and connecting rod from my engine and spin the crank by hand, it will run long enough for me to go into the house, put the kettle on, and return to the workshop to find it is still spinning.
I have no wish to hijack your thread but the following information may well be of value to you and others. The tests were to establish the effect of the 'Choke' on the engines performance and the results are quite enlightning. The best by far was the original cooler head with 80 x 1.2mm holes yet I was/am puzzled as to why the plain choke failed to improve the performance. Still thinking about the results!
Appologies for the quality of the graph, I had to photograph the computer screen as the forum won't accept a PDF file.
GeoffV
Re: large lamina flow build
Hey Geoff (and anyone interested),
I know its way off subject, but here's some freeware/software that i use to capture screenshots. I've been using it for a couple years without fail.
You can choose multiple capture size/options, file types, destinations, hot keys, cropping etc.
It's called Gadwin Printscreen..
http://www.gadwin.com/download/

This is the particular software/freeware download box to choose from once you've opened the link.
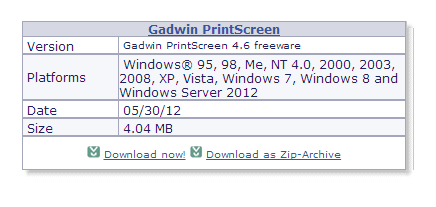
It's near the bottom of the page.
I highly recommend it to everyone.
Its just like taking a photo...xept better!
vamoose
I know its way off subject, but here's some freeware/software that i use to capture screenshots. I've been using it for a couple years without fail.
You can choose multiple capture size/options, file types, destinations, hot keys, cropping etc.
It's called Gadwin Printscreen..
http://www.gadwin.com/download/

This is the particular software/freeware download box to choose from once you've opened the link.
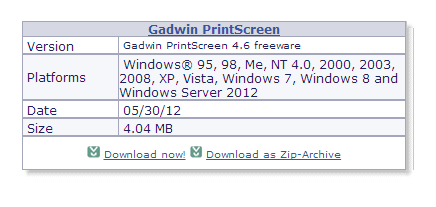
It's near the bottom of the page.
I highly recommend it to everyone.
Its just like taking a photo...xept better!
vamoose
Re: large lamina flow build
Derwood
Apologies for the distraction.
Vamoose
Thanks for the link, it works well.
GeoffV
Apologies for the distraction.
Vamoose
Thanks for the link, it works well.
GeoffV
Re: large lamina flow build
It is not a distraction.Geoff V wrote:Apologies for the distraction.
Re: large lamina flow build
I have stumbled on to something interesting pertaining to choke size. As I have said, results have been conflicting. I have realized why. The first cylinder I was using was old and a bit warped. It had a 1/4 inch steel plate welded to the cylinder at one end (the head). I switched to a new cylinder for a better seal and made a new head that bolted on. When I started testing again, I had to go to a larger choke to get it to run. Start up time was much quicker but the rpms were low. this is the head used in the video. I then made another head that would accept larger diameter chokes because I thought a larger choke might improve performance. It would not run with the larger choke. I then went back to the choke size that made it run, but now it would not run. The engine showed signs of much higher power but compression seemed way to high. I went to a smaller choke and now it is so close to running, that adding weight to the flywheel or lowering compression will probably do the trick. The difference is that the first bolt on head was made from ss and the latest is mild steel. I used ss because I thought it would serve as a good heat break and it did because start up was much quicker. It also lowered the cooling effect in the cylinder which lowered power. The mild steel head slows the start up time but seems to increase the power. Also when I increase the the heat it displays an increase in power but with the ss head it would not show power increase. It seems that the amount of cooling taking place in the cylinder has a direct effect on choke size. It is obvious to me that the compression ratio needed is determined not only by the the heat exchange in the hot tube but also in the cylinder. The mild steel head uses a 9/16 in. choke and the ss head required a 13/16 in. choke. All other conditions were exactly the same during these tests. An aluminum head would probably increase power and a heat break is needed where the choke meets the head. I had no idea that head material would make such a big difference in power.Geoff V wrote:The tests were to establish the effect of the 'Choke' on the engines performance and the results are quite enlightning. The best by far was the original cooler head with 80 x 1.2mm holes yet I was/am puzzled as to why the plain choke failed to improve the performance. Still thinking about the results!
Also I have thought alot about your TL engine and how your design works. I think it is possible that the small space between the outer and inner tube acts as the choke. The perferated aluminum head increases cooling in the cylinder and is much needed. Maybe you should try keeping the aluminum head and try to incorporate some type of choke system between the heat tube and the head.
Thanks for the input,
Derwood
Re: large lamina flow build
Derwood
I believe I now understand why your engine is so dependant on choke size, FRICTION, if I may expand my thoughts.
From my test results, the choke produces a more 'peaky' curve and slightly less power than the tubular cooler head and changing the choke size in small increments demonstrates that there is an optimum size for best power. If the friction in your linkage is just less than the power developed, your engine will only 'self sustain' when presented with the optimum choke size and will be reluctant to run at a speeds much above or below the speed at which the peak power occurs.
The coefficient of friction for rotating shaft plastic bearings is difficult to establish but is in the range of 0.1 to 0.15 where as deep groove ball races with very low viscosity lubricant (WD40 for example) can be as low as 0.001 or one hundreth that of a plastic bearing!!!!!!!!!!!!
Before dismantling my test bed I tried a variety of changes in the search for improvements (non found yet!) and the only change that stopped the engine running was by reducing the pulse tube volume by about 1/3. Other changes included SS foil regenerator matrix instead of the SS scouring pad and as already stated removing the choke all together, these changes reduced the peak power but the engine still started easily and ran 'sweetly'.
As mentioned in a previous reply my engine has very low friction, any more friction would not only reduce peak power at the Prony brake but would also require the best combination of choke size, pulse tube volume, regen matrix etc. etc.
I hope my thought are of value to you.
GeoffV
I believe I now understand why your engine is so dependant on choke size, FRICTION, if I may expand my thoughts.
From my test results, the choke produces a more 'peaky' curve and slightly less power than the tubular cooler head and changing the choke size in small increments demonstrates that there is an optimum size for best power. If the friction in your linkage is just less than the power developed, your engine will only 'self sustain' when presented with the optimum choke size and will be reluctant to run at a speeds much above or below the speed at which the peak power occurs.
The coefficient of friction for rotating shaft plastic bearings is difficult to establish but is in the range of 0.1 to 0.15 where as deep groove ball races with very low viscosity lubricant (WD40 for example) can be as low as 0.001 or one hundreth that of a plastic bearing!!!!!!!!!!!!
Before dismantling my test bed I tried a variety of changes in the search for improvements (non found yet!) and the only change that stopped the engine running was by reducing the pulse tube volume by about 1/3. Other changes included SS foil regenerator matrix instead of the SS scouring pad and as already stated removing the choke all together, these changes reduced the peak power but the engine still started easily and ran 'sweetly'.
As mentioned in a previous reply my engine has very low friction, any more friction would not only reduce peak power at the Prony brake but would also require the best combination of choke size, pulse tube volume, regen matrix etc. etc.
I hope my thought are of value to you.
GeoffV
Re: large lamina flow build
Friction Is always an issue. Ball bearings would be a better choice but the fly wheel spins freely. When i spin it by hand without linkage it keeps turning for a good bit of time. When the engine is running I can grab the crank shaft and squeeze it firmly and the engine keeps running. After more testing I feel that the choke is compensating for low heat exchange in the heat tube. The ss head slows the heat transfer to the cylinder. The transition from hot to cold is more sudden. The mild steel head pulls heat into the cylinder much faster and the transition from hot to cold is spread out over a longer distance and basically diffuses the whole process. With the ss head the choke heats up quicker and the cylinder is still cool when the engine begins to run. With the mild steel head the cylinder is very warm by the time the choke area heats up enough to show signs of life. A heat break seems to be very important and the mild steel head might work better if there was an effective heat break where the choke meets the head. As far as power increase goes, It is clear to me now that improved heat exchange is the only way to increase the power. Even with an improved heat exchanger I think the power increase would be small. I could get more rpms of course with a shorter stroke but I think I will continue to test with the current stroke.
Re: large lamina flow build
For anyone who is interested in building this type of engine, A heat break proves to be very important. I added a heat break between the heat tube and the cylinder and now the engine runs with the mild steel head and choke size was increased to 1 1/4 in. Power output is about the same and rpms are just a little faster. I think it is time to modify the heat tube for better heat exchange and play with the compression ratio.
Re: large lamina flow build
If you arn't all ready, it might be worth thinking about water cooling now, either a gravity, trickle system,or a thermosyphon. Getting rid of heat is at least as important as getting the heat in at the other end.
Ian S C
Ian S C
Re: large lamina flow build
Yes, I am going to use a drip system very soon just to see if a power increase results.
When I started this project my cylinder to heat tube ratio was about 5.75. I am now down to 3 and I think it needs to lower even more. Last night I started using a 1.75 in. diameter heat tube. I was using a 2.8 diameter heat tube in the video. The results are positive, a noticeable power increase was observed. I think compression is still too low. The smaller i.d. tube seems to do a better job heating the air. The volume of the smaller tube was the same as the larger tube but the engine ran smoother and at a slightly higher rpm. I am now up to 130 rpms. Torque is surprisingly high.
When I started this project my cylinder to heat tube ratio was about 5.75. I am now down to 3 and I think it needs to lower even more. Last night I started using a 1.75 in. diameter heat tube. I was using a 2.8 diameter heat tube in the video. The results are positive, a noticeable power increase was observed. I think compression is still too low. The smaller i.d. tube seems to do a better job heating the air. The volume of the smaller tube was the same as the larger tube but the engine ran smoother and at a slightly higher rpm. I am now up to 130 rpms. Torque is surprisingly high.
Re: large lamina flow build
Correct me if I am wrong but I was thinking that my engine is 210 cc. Isn't the displacment half of the total stroke volume. I have to bleed off the pressure at half stroke at start up, so I am assuming that only half of the total volume is being displaced.