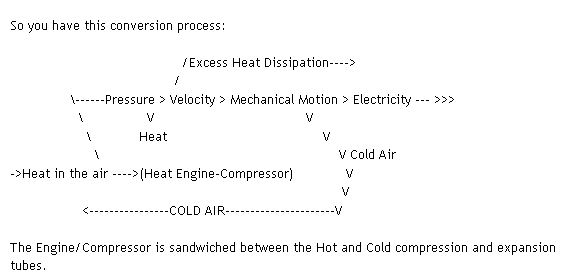
Stirling Turbine
Re: Stirling Turbine
This was what the original diagram posted above was supposed to look like:
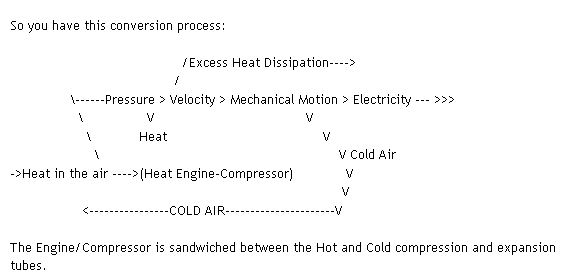
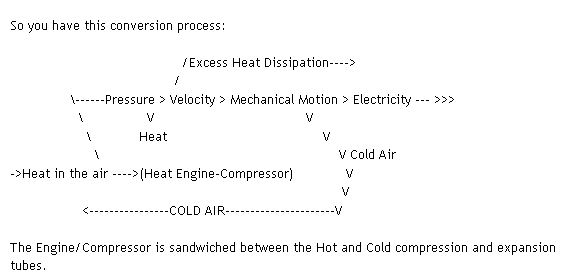
Re: Stirling Turbine
Hi Tom. I didn't know that about Tesla. Good company indeed. I don't know if I understand you to mean that you could collect energy by simply exhausting the cold gas - the temp drop doesn't represent power until it collects ambient heat, a process that would in that case happen externally and be totally lost. If it's possible for a heat engine to make its own temperature difference and run on ambient heat from its cold side, I would think the principle would be to draw off all of the heat under compression, replace it with ambient heat on expansion, and then add back the initially removed heat for power. In a piston engine example, you probably couldn't raise the power stroke peak temperature/pressure, but perhaps you could raise it's average. In your case I see a closed loop, exhausting the cold gas from the turbine around one end of your thermal/displacer/compressor to provide its temp difference, and then into the compressor. The "warm" end of the compressor would be very cold; a harvesting point for ambient heat/energy. You've still got the problem of where to put the heat of your compressed gas - I'm getting a headache.
Years ago I spent a lot of time on ambient heat engine theory and even made a couple of piston engine models which didn't prove or disprove anything since the friction was too high. I did notice temperature differences along the exchanger went in the direction I wanted to see, but that's all I ever accomplished. Funny, those two versions were remarkably similar mechanically to some of the thermal lag/lamina engines I see now. At any rate, I still believe it can be done. I wish you well with your project.
Years ago I spent a lot of time on ambient heat engine theory and even made a couple of piston engine models which didn't prove or disprove anything since the friction was too high. I did notice temperature differences along the exchanger went in the direction I wanted to see, but that's all I ever accomplished. Funny, those two versions were remarkably similar mechanically to some of the thermal lag/lamina engines I see now. At any rate, I still believe it can be done. I wish you well with your project.
Re: Stirling Turbine
Bumpkin wrote: I don't know if I understand you to mean that you could collect energy by simply exhausting the cold gas - the temp drop doesn't represent power until it collects ambient heat, a process that would in that case happen externally and be totally lost.
My understanding of gas under pressure is that the pressure (PSI) would be more or less equally distributed along the walls of the long tube that the "compressor" is pumping air into regardless of temperature changes along the way.
The air, however, is being continually cooled as it travels down the tube. Therefore, contracting and loosing pressure along the way. What you would have exiting the tube into the turbine would be very dense cool air but presumably the very hot air behind it would tend towards lending pressure to it as the pressure should be equal at any point.
My understanding; due to studying the principles involved in gas liquefaction which uses a similar process of compression and pre-cooling of a gas and injection of that pre-cooled condensed gas into a turbine; is that the condensed gas is in a sense "wound up" or actually "compressed" not by pressure so much as by cooling, like a compressed spring and when released into the turbine through a nozzle the cool compressed air expands rather explosively, like a spring suddenly released, and so powers the turbine.
The gas or compressed air, once released, requires HEAT in order to expand.
If the turbine is well insulated, NO EXTERNAL HEAT IS AVAILABLE for it to draw upon for energy to do the expanding. Regardless, the gas expands rapidly anyway and does power the turbine by such expansion drawing upon its own "INTERNAL LATENT HEAT" to do so.
I am not a Physicist and so can not say exactly how or why this happens, but the result is that the gas, having thus expanded, in spite of no external heat being available to do the expanding, drops in temperature precipitously due to being forced to draw upon it's own INTERNAL HEAT RESERVE. Remember that the gases in the air contain a great deal of latent heat well below ambient temperatures.
There is no "Ambient Heat" involved at this point. None is available. More than likely the COOL pressurized air, as it is released into the turbine is alredy BELOW AMBIENT. So where does the power to turn the turbine come from? From the latent internal molecular heat within the gas or air itself. This is somewhat difficult to conceptualize but it is a process in common use today, even now as we speak. It is used in various cooling processes, air-cycle refrigeration, gas liquefaction, cryogenics, refining processes, etc. etc.
One of the reasons it (the "expansion turbine") is so widely used is that much of the energy to compress the air is recovered when it is then re-expanded through the turbine. Like compressing a spring and letting it go again.
But under ordinary circumstances it takes more energy to compress the air than you get back when it expands. Conventional compressors generally eat and waste a lot of power. Theoretically though, a compressor that runs on ambient heat would have a virtually inexhaustible reserve of energy to draw upon, so if you only get 10% back at the turbine that is 10% of freely available, inexhaustible ambient/solar heat/energy.
Re: Stirling Turbine
Just to be clear, the ambient side would be the HOT side.Bumpkin wrote:... If it's possible for a heat engine to make its own temperature difference and run on ambient heat from its cold side,
If I follow your reasoning correctly, Yes, I agree.I would think the principle would be to draw off all of the heat under compression, replace it with ambient heat on expansion, and then add back the initially removed heat for power.
As I mentioned earlier the engine illustrated in the animated drawing is an "exploded view" intended to make all the components visible and the whole process, hopefully, comprehensible.
Originally I had the turbine situated INSIDE the displacer chamber where the cooling tubes are shown so as to reabsorb heat that makes its way through the chamber directly. Also there could be some baffles on the underside to allow the reintroduction of some ambient heat at the turbine nozzles which could be equipped with pre-heaters. This extra heat at the turbine would increase the rate of expansion and so increase power output. However there would be a trade off in that with the reintroduction of ambient heat you would loose some of your temperature differential, though if the turbine is already cold enough, or conceivably TOO COLD (these expansion turbines are intended for reaching ultra-cold cryogenic temperatures in many applications) the reintroduction of some heat at the turbine would be desirable. This would, however have to be carefully regulated I imagine.
I think this is getting a bit ahead of ourselves though.
At this point I'm still working on developing some sort of functional heat driven compressor. I'm fairly certain that a simple displacer chamber would not be able to reach compression levels sufficient to cause the release of much heat or to power a turbine. Most likely the pressure would have to be stepped up somehow. This would be easy enough I believe but would probably entail the reintroduction of additional mechanisms for the purpose which would increase the number of moving parts, friction and so forth.
Some sort of simple hydraulics could step up the pressure but would more than likely simultaneously decrease the volume of air flow.
At any rate, if it can be gotten working at all, then there would certainly be room for increasing efficiency and power output in various ways.
One possibility I've been considering lately is to use a sealed displacer chamber. The incoming air does not necessarily have to pass through the chamber. A closed air-cycle system has also been developed recently which would solve a number of problems like water condensation and ice formation. In a closed system compressed DRY AIR could be used.
I was also thinking that the pressure from a displacer chamber might be increased if some sort of liquid could be used. Possibly a mixture of water and ammonia, though in any case it would be preferable to avoid the use of chemicals or conventional refrigerants IMO.
But at any rate my reasoning is that ammonia gas can rather easily escape from and be re-absorbed by water with changes in temperature. How ammonia based refrigerators work.
Heated, the ammonia escapes from the mixture creating pressure, cooled it is reabsorbed. Just how practical an idea that might be I don't know. I imagine as the mix is forced to the hot side, the ammonia escaping and forming bubbles in the mix causing tremendous pressure, when forced to the cold side the ammonia bubbles are reabsorbed causing contraction. Or perhaps some other non-compressible liquid with a high expansion ratio could be used, though for the time being I think I would like to see how it works using plain old air. As I say, if the concept can be demonstrated as workable, however inefficient, there should be plenty of room for innovation and improvement down the line.