A lighter weight solution could be a nylon ball and socket joint like those used in RC cars and planes. Should work for the smaller engines.
Power piston sideloading: possible solutions
Power piston sideloading: possible solutions
I was wondering if anyone had tried this on a large engine. Using a u-joint type coupling to the power piston. The picture is that of a cylinder hone, but you get the idea. It was meant to prevent sideloading and insure a smooth movement. This way, the power piston can stay concentric in the bore and reduce the friction as well as increase the speed due to the same fact. The downside is that it adds a little weight to the piston and rod. But if you don't feel like lapping another piston in the bore and like the part to live longer....this might be a solution. I won't be using it for my v-twin stirling, because everything is already laid out perfect for me. It would allow a quick and dirty build for prototypes, though.
A lighter weight solution could be a nylon ball and socket joint like those used in RC cars and planes. Should work for the smaller engines.
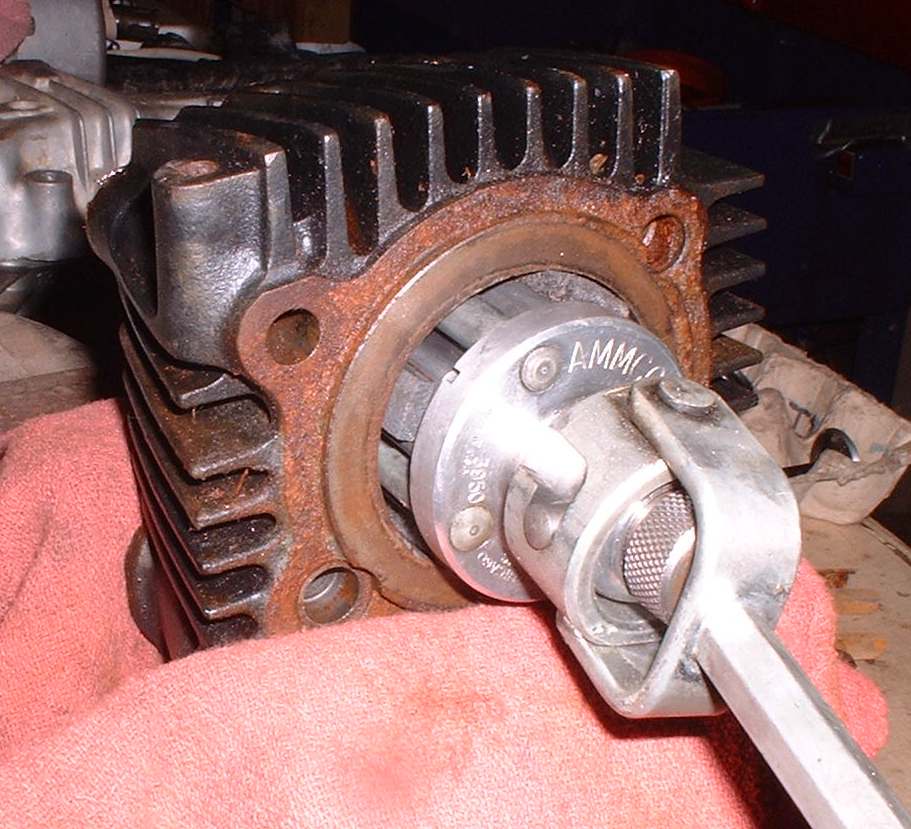
A lighter weight solution could be a nylon ball and socket joint like those used in RC cars and planes. Should work for the smaller engines.

Re: Power piston sideloading: possible solutions
With my BETA type motors I try to do something similar, or you tend to get a bit sideways, the important thing is to get the con rod as long as possible, to keep the angle to a minimum, hense the advantage of the "Ross Yoke". or the "scotch yoke"and the rhombic drive, all keeping the thrust angle to zero.
another cause of bad loading on a piston is attaching it in a similar fashon to your hone, its better that the gudgion pin is about half way down the length of the piston, like a car, or other IC engine piston, you can do that with metal pistons, and I think it would be possible with a graphite one as long as its not too small. For my last engineI made the cast iron piston that way, bore 3/8", its a beam engine with a stroke of 1/2". Ian S C
another cause of bad loading on a piston is attaching it in a similar fashon to your hone, its better that the gudgion pin is about half way down the length of the piston, like a car, or other IC engine piston, you can do that with metal pistons, and I think it would be possible with a graphite one as long as its not too small. For my last engineI made the cast iron piston that way, bore 3/8", its a beam engine with a stroke of 1/2". Ian S C
Last edited by Ian S C on Sun Mar 11, 2012 3:07 am, edited 1 time in total.
Re: Power piston sideloading: possible solutions
Those airpots made by airpot corporation have a ball joint to minimize the side loading. Probably one of the
reasons they're so smooth.
reasons they're so smooth.
http://www.scraptopower.co.uk My web site, Stirling engines and AE stuff.